Existuje celá řada výrobních procesů pro výrobu azakázková kovová část. Každý má svůj vlastní soubor výhod a nevýhod. Některé z důležitých faktorů ovlivňujících výběr procesu zahrnují následující:
- Množství požadovaného materiálu
- Design kovové části
- Požadované tolerance
- Specifikace kovu
- Vyžaduje povrchovou úpravu
- Náklady na nástroje
- Ekonomika obrábění versus procesní náklady
- Požadavky na dodání
Casting
Proces odlévání spočívá v lití nebo vstřikování roztaveného kovu do formy obsahující dutinu s požadovaným tvaremodlitky. Procesy lití kovů lze klasifikovat buď podle typu formy nebo podle tlaku použitého k plnění formy tekutým kovem. Pokud podle typu formy, proces odlévání by mohl být klasifikován na lití do písku, lití na vytavitelné odlévání a lití kovů pod tlakem; zatímco tlak použitý k plnění formy by mohl být proces odlévání rozdělen na gravitační lití, nízkotlaké lití a vysokotlaké lití.
Základy castingu
Lití je proces tuhnutí. Proto může být mikrostruktura jemně vyladěna, jako je struktura zrn, fázové transformace a precipitace. S tuhnutím jsou však úzce spojeny také defekty, jako je poréznost smršťování, praskliny a segregace. Tyto vady mohou vést ke snížení mechanických vlastností. Pro snížení zbytkového napětí a optimalizaci mechanických vlastností je často vyžadováno následné tepelné zpracování.
Výhody castingu:
- Velké a složité výrobky odlévání kovů jsou snadné.
- Vysoká rychlost výroby, speciálně automatickou formovací linkou.
- Flexibilita designu je dostupná a vhodnější.
- Dostupné různé kovy: šedá litina, tvárná litina, uhlíková ocel, legovaná ocel,nerez, slitina hliníku, mosaz, slitina bronzu a zinku.
Nevýhody castingu:
- Vady uvnitř odlitků
- Smršťovací pórovitost
- Kovové výstupky
- Praskliny, trhání za tepla, studené uzávěry
- Kola, oxidy
- Chybné běhy, nedostatečný objem
- Inkluze
- Vyžaduje pečlivou kontrolu procesu a kontroly (může se objevit pórovitost)
Kování
Kování je výrobní proces, kde je kov tvarován plastickou deformací pod velkým tlakem do vysoce pevných dílů. Podle toho, zda se použije kovací forma, se proces kování začlení do otevřeného zápustkového kování a uzavřeného zápustkového kování. Pokud však podle teploty kovaného kovu a slitiny před kováním lze proces kování rozdělit na kování za studena, kování za tepla a kování za tepla.
Základy kování
Kování nebo tváření za studena jsou procesy tváření kovů. Nedochází k tavení a následnému tuhnutí. Plastická deformace způsobuje zvýšení počtu dislokací, což má za následek vyšší stav vnitřního napětí. Deformační zpevnění je skutečně připisováno interakci dislokací s jinými dislokacemi a jinými bariérami (jako jsou hranice zrn). Současně se po plastickém opracování kovu mění tvar primárních krystalů (dendritů).
Výhody kování:
- Dobré mechanické vlastnosti (mez kluzu, tažnost, houževnatost)
- Spolehlivost (používá se pro kritické díly)
- Žádná úprava tekutých kovů
Nevýhody kování:
- Zemřít nevyplnit
- Selhání zemřít
- Tvar omezený, když jsou vyžadovány podříznutí nebo dutinkové sekce
- Celkové náklady jsou obvykle vyšší než odlévání
- Často je vyžadováno více kroků
Rozeznáváme práci za tepla od tváření za studena. Zpracování za tepla se provádí nad teplotou rekrystalizace; pod ním se provádí opracování za studena. Při práci za tepla jsou deformační zpevnění a deformovaná struktura zrna velmi rychle eliminovány tvorbou nových zrn bez pnutí v důsledku rekrystalizace. Rychlá difúze při vysokých pracovních teplotách napomáhá homogenizaci předlisku. Počáteční pórovitost lze také výrazně snížit, případně zcela zhojit. Metalurgické jevy, jako je deformační zpevnění a rekrystalizace, jsou důležité, protože tyto změny ve struktuře mají za následek zvýšení tažnosti a houževnatosti v odlitém stavu.
Důležité je mít na paměti, že kvalita materiálů a tepelné zpracování může být v některých případech důležitějším faktorem než rozdíl mezi litím a kováním.
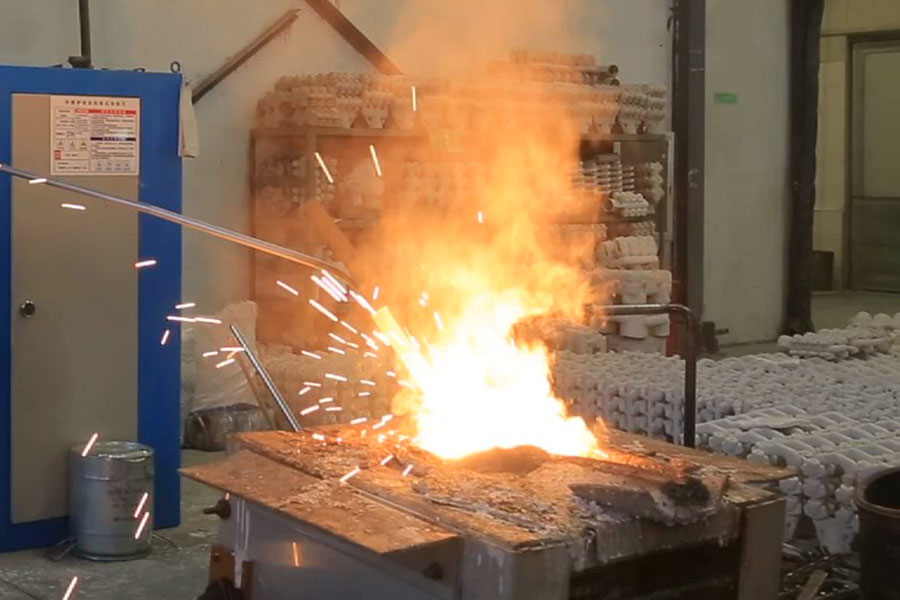
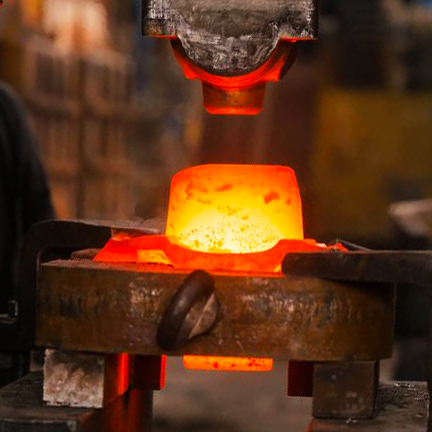
Čas odeslání: 24. února 2021