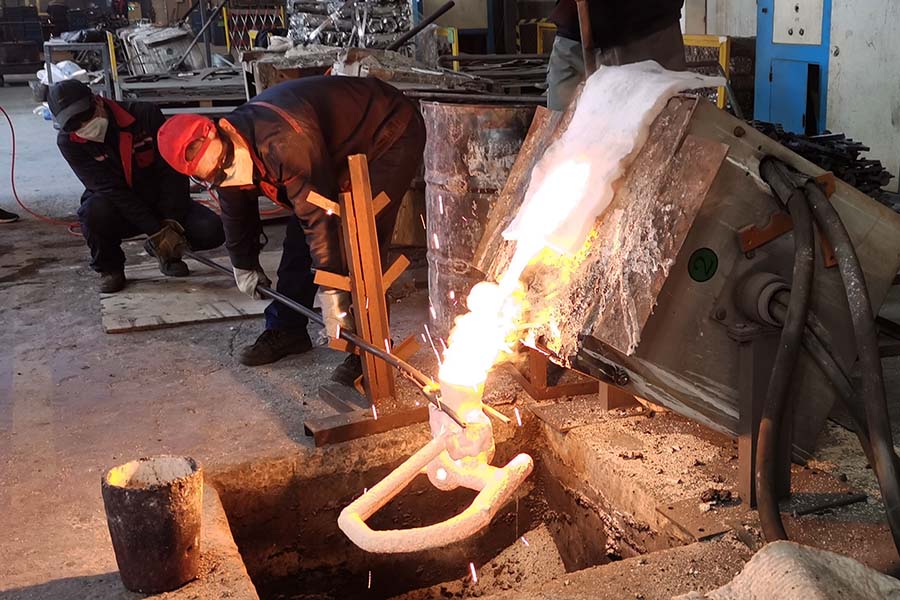
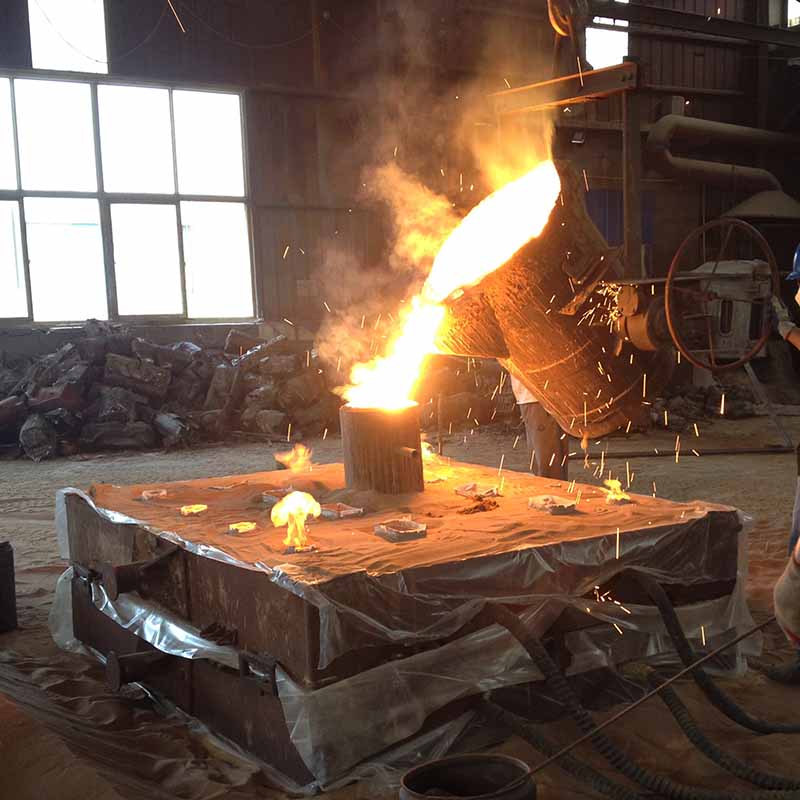
Odlévání je jednou z prvních metod tváření kovů, které lidé znali. Obecně to znamená nalití roztaveného kovu do žáruvzdorné formy s dutinou tvaru, který má být vyroben, a nechat ji ztuhnout. KdyžPo ztuhnutí se požadovaný kovový předmět vyjme ze žáruvzdorné formy buď rozbitím formy, nebo rozebráním formy. Ztuhlý předmět se nazývá odlévání. Tento proces se také nazývá zakládání a nazývá se moderní továrna, která se zaměřuje na odlévání kovových dílůslévárna.
1. Historie odlévacího procesu
Proces odlévání byl pravděpodobně objeven kolem roku 3500 před naším letopočtem v Mezopotámii. V mnoha částech světa se v tomto období měděné sekery a další ploché předměty vyráběly v otevřených formách vyrobených z kamene nebo pálené.jíl. Tyto formy byly v podstatě z jednoho kusu. Ale v pozdějších obdobích, kdy bylo nutné vyrábět kulaté předměty, byly takové formy rozděleny na dvě nebo více částí, aby se usnadnilo vyjmutí kulatých předmětů.Doba bronzová (asi 2000 př. n. l.) přinesla do odlévacího procesu mnohem více zdokonalení. Snad poprvé bylo vynalezeno jádro pro vytváření dutých kapes v předmětech. Tato jádra byla vyrobena z pálené hlíny.Také proces cire perdue nebo ztraceného vosku byl široce používán pro výrobu ozdob a jemné práce.
Technologii odlévání značně zdokonalili Číňané od doby kolem roku 1500 před naším letopočtem. Předtím neexistují žádné důkazy o tom, že by se v Číně nacházela nějaká odlévací činnost. Nezdá se, že by byli skvělíobeznámeni s procesem cire perdue, ani jej široce nepoužívali, ale místo toho se specializovali na vícedílné formy pro vysoce složité práce. Strávili spoustu času zdokonalováním formy do posledního detailu, takže sotvana odlitku vyrobeném z forem byly nutné jakékoliv dokončovací práce. Pravděpodobně vyráběli kusové formy obsahující pečlivě osazené kusy v počtu třiceti nebo více. Ve skutečnosti bylo objeveno mnoho takových foremarcheologické vykopávky v různých částech Číny.
Civilizace údolí Indus je také známá svým rozsáhlým používáním odlévání mědi a bronzu pro ozdoby, zbraně, nástroje a náčiní. Ale v technologii nebylo mnoho zlepšení. Z variU předmětů a figurek, které byly vykopány z nalezišť v údolí Indus, se zdá, že znali všechny známé metody odlévání, jako je otevřená forma, kusová forma a proces cire perdue.
Ačkoli Indie mohla být připsána za vynález kelímkové oceli, v Indii nebylo příliš mnoho z nakládání železa. Existují důkazy, že železářství začalo kolem roku 1000 př.nl v Sýrii a Persii. Objeví seželití železatechnologie v Indii se používala od dob invaze Alexandra Velikého, kolem roku 300 před naším letopočtem.
Slavný železný sloup, který se v současnosti nachází poblíž mináru Qutb v Dillí, je příkladem metalurgických dovedností starých Indů. Je dlouhý 7,2 m a je vyroben z čisté kujné litiny. Předpokládá se, že toto je zobdobí Chandragupta II (375-413 n. l.) z dynastie Guptů. Míra rezivění tohoto sloupu, který stojí venku pod širým nebem, je prakticky nulová a dokonce i zakopaná část rezaví extrémně pomalu. Tentomusel být nejprve odlit a poté vytlučen do konečného tvaru.
2. Výhody a omezení
Proces odlévání je široce používán ve výrobě, protože má mnoho výhod. Roztavený materiál proudí do jakékoli malé části v dutině formy a jako takový má jakýkoli složitý tvar – vnitřnínebo externí – lze vyrobit procesem odlévání. Je možné odlévat prakticky jakýkoli materiál, železný i neželezný. Dále, potřebné nástroje potřebné pro odlévací formy jsou velmi jednoduché alevný. Ve výsledku je to ideální metoda pro zkušební výrobu nebo výrobu malého množství. V procesu odlévání je možné umístit množství materiálu tam, kde je přesně požadováno. V důsledku toholze dosáhnout snížení hmotnosti v designu.Odlitkyjsou obecně chlazeny rovnoměrně ze všech stran, a proto se očekává, že nebudou mít žádné směrové vlastnosti. Existují určité kovy a slitinykteré lze zpracovávat pouze odléváním a ne žádným jiným procesem, jako je kování, z důvodu metalurgických důvodů. Lze vyrobit odlitky libovolné velikosti a hmotnosti, dokonce až 200 tun.
Nicméně rozměrová přesnost a povrchová úprava dosahují normálníproces lití do pískuby v mnoha případech nebylo pro konečnou aplikaci dostačující. Abychom tyto případy vzali v úvahu, nějaké speciální odléváníbyly vyvinuty procesy, jako je tlakové lití, jejichž podrobnosti jsou uvedeny v dalších kapitolách. Také proces lití do písku je do určité míry náročný na práci, a proto je na něj zaměřeno mnoho vylepšení,jako je strojní formování a slévárenská mechanizace. U některých materiálů je často obtížné odstranit vady způsobené vlhkostí přítomnou v nichpískové odlitky.
3. Podmínky castingu
V následujících kapitolách budou uvedeny podrobnosti o lití do písku, které představuje základní proces lití. Než se pustíme do podrobností tohoto procesu, bylo by třeba definovat několik slovíček ve slovní zásoběpřivlastnit si.
Baňka– Formovací baňka je taková, která drží pískovou formu neporušenou. V závislosti na poloze formovacího rámu ve struktuře formy je označována různými názvy, jako je drag, cope a cheek. Je vyrobena ze dřevapro dočasné použití nebo obecněji z kovu pro dlouhodobé použití.
Táhnout– Spodní formovací baňka
Vyrovnat se– Horní formovací baňka
Tvář– Meziformovací baňka používaná při třídílném formování.
Vzor– Vzor je replikou finálního objektu, který má být vyroben s určitými úpravami. Dutina formy je vyrobena pomocí vzoru.
Dělící čára– Toto je dělicí čára mezi dvěma formovacími baňkami, která tvoří pískovou formu. U děleného vzoru je to také dělicí čára mezi dvěma polovinami vzoru
Spodní deska– Jedná se o desku obvykle vyrobenou ze dřeva, která se používá na začátku výroby formy. Vzor se nejprve podrží na spodní desce, nasype se na ni písek a poté se provede pěchování v tahu.
Tváří v tvář písku– Malé množství uhlíkatého materiálu nastříkaného na vnitřní povrch dutiny formy pro lepší povrchovou úpravu odlitků
Formovací písek– Je to čerstvě připravený žáruvzdorný materiál používaný pro výrobu dutiny formy. Je to směs křemičitého jílu a vlhkosti ve vhodných poměrech pro dosažení požadovaných výsledků a obklopujevzor při výrobě formy.
Podkladový písek– Je to to, co tvoří většinu žáruvzdorného materiálu nacházejícího se ve formě. Tu tvoří použitý a pálený písek.
Jádro– Používá se pro výrobu dutých dutin v odlitcích.
Nalévací pánev– Malá trychtýřovitá dutina v horní části formy, do které se nalévá roztavený kov.
Spurný– Průchod, kterým se roztavený kov z licí vany dostává do dutiny formy. V mnoha případech řídí tok kovu do formy.
Běžec– Průchody v dělicí rovině, kterými se reguluje proudění roztaveného kovu, než se dostane do dutiny formy.
Brána– Skutečný vstupní bod, kterým roztavený kov vstupuje do dutiny formy.
Věnec– Čepele se používají k podepření jader uvnitř dutiny formy, aby se postaraly o vlastní hmotnost a překonaly metalostatické síly.
Chlad– Chladničky jsou kovové předměty, které se umísťují do formy, aby zvýšily rychlost ochlazování odlitků a zajistily rovnoměrnou nebo požadovanou rychlost ochlazování.
Stoupačka– Jedná se o zásobník roztaveného kovu umístěný v odlitku tak, aby horký kov mohl proudit zpět do dutiny formy, když dojde ke zmenšení objemu kovu v důsledku tuhnutí
4. Postup výroby pískové formy
Postup výroby typické pískové formy je popsán v následujících krocích:
Nejprve se na formovací plošinu nebo na podlahu položí spodní deska, čímž se povrch vyrovná. Tažná formovací baňka je držena dnem vzhůru na spodní desce spolu s tažnou částívzor ve středu baňky na desce. Mezi vzorem a stěnami baňky by měla být dostatečná vzdálenost, která by měla být řádově 50 až 100 mm. Suchý obkladový písek se posypedeska a vzor poskytují nelepivou vrstvu. Čerstvě připravený formovací písek požadované kvality se nyní nasype do vleku a na model v tloušťce 30 až 50 mm. Zbytek záchytné baňky jezcela naplněna záložním pískem a rovnoměrně udusaná, aby se písek zhutnil. Utloukání písku by mělo být provedeno správně, aby se příliš nezhutnil, což ztěžuje únik plynů,ani příliš volné, aby forma neměla dostatečnou pevnost. Po ukončení pěchování se přebytečný písek v baňce zcela seškrábe pomocí ploché tyče na úroveň okrajů baňky.
Nyní, s odvzdušňovacím drátem, což je drát o průměru 1 až 2 mm se špičatým koncem, jsou ve vleku vytvořeny ventilační otvory do celé hloubky baňky a také do vzoru, aby se usnadnilo odstranění plynů. během odlévánítuhnutí. Tím je příprava tahu dokončena.
Hotová baňka se nyní převalí na spodní desku a odkryje vzor, jak je znázorněno na fotografii. Pomocí slicku se okraje písku kolem vzoru opraví a překryje se vrchní polovina vzorutahový vzor, zarovnejte jej pomocí kolíků. Horní baňka na horní části tažení je umístěna tak, aby byla opět vyrovnána pomocí kolíků. Suchý dělicí písek je posypán po celé brzdě a na vzoru.
V malé vzdálenosti asi 50 mm od vzoru je umístěn vtokový kolík pro vytvoření průchodu vtokového kanálu. V případě potřeby je také na vhodném místě uložen nástavec a čerstvě připravený formovací písek podobný tomutahu spolu s podkladovým pískem se posype. Písek se důkladně udusá, přebytečný písek se seškrábe a po celém výkopu se udělají větrací otvory jako u brzdy.
Vtokový kolík a stoupací kolík se opatrně vyjmou z baňky. Později se vylévací nádrž prořízne poblíž vrcholu vtoku. Vršek je oddělen od brzdy a veškerého sypkého písku na rozhraní vršku a brzdyodpor je odfouknut pomocí měchů. Nyní jsou poloviny vršku a vlečného vzoru staženy pomocí tažných hrotů a klepáním vzoru kolem dokola, aby se mírně zvětšila dutina formy, takžestěny formy nejsou poškozeny utahovacím vzorem. Lišty a vrátka jsou ve formě pečlivě vyříznuty, aniž by se forma znehodnotila. Jakýkoli přebytečný nebo uvolněný písek nalezený v žlabech a dutině formy je vyfoukánpryč pomocí měchu. Nyní se po celé dutině formy a žlabech nanese obkladový písek ve formě pasty, což dodá hotovému odlitku dobrou povrchovou úpravu.
Suché pískové jádro se připraví pomocí jaderníku. Po vhodném upečení se umístí do dutiny formy, jak je znázorněno na fotografii. Vršek je vyměněn na brzdě, přičemž se stará o vyrovnání obou pomocíšpendlíky. Na vršku je udržováno vhodné závaží, aby se postaralo o vzestupnou metalostatickou sílu během lití roztaveného kovu. Forma je nyní, jak je znázorněna na fotografii, připravena k lití.
Čas odeslání: 25. prosince 2020